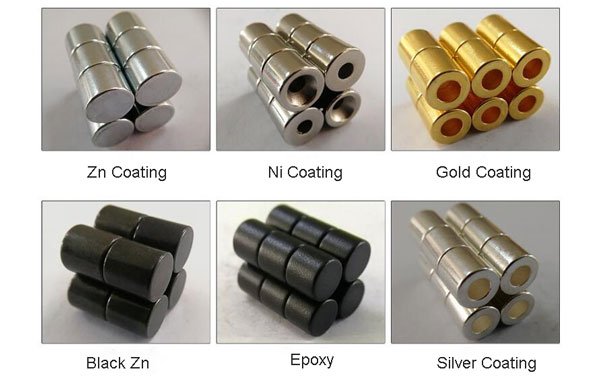
neodymium magnet coating
Reason: Prevent oxidation and corrosion, extend magnet lifespan
Key factors: waterproof, UV resistance, friction, insulation, biocompatibility
Single-layer coatings: Ni, Zn, Au, Sn, Ti, TiN, Epoxy, PTFE, Parylene
Multi-layer coatings: Ni-Cu-Ni, Ni-Cu-Ni+PTFE, Zn+Rubber, Tin+Parylene
Why need Coating & Plating?
Neodymium magnet coating is one of the main factors in production. Because the materials of neodymium magnets are unstable since they contain a lot of iron. They can have negative chemical reactions – corrosion (rust) – under hot and humid working conditions. This will weaken the magnetic performance and even shorten their life spans. And the coating can prevent or slow down oxidation very well.
What should be considered when choosing a coating
In many cases, people just consider how to make sure the neodymium magnet will not rust. But in some high technology cases or medical cases, there are many factors should be conisder, likes:
- waterproof
- Mildew-proof
- Strong anti-salt spray performance
- Coefficient of friction
- Operating temperature
- Improved UV resistance
- Uniform thickness
- No damage to the workpiece
- Electrical insulation
- Biological evaluation of medical devices
- Comply with the biological test requirements of UDP Class VI plastics
How many kinds of magnet coating?
There are many standards for distinguishing coatings, and Osenc mainly divided into two types:
One layer coating
Nickel (Ni)
Zinc (Zn)
Gold (Au)
Tin (Sn)
Titanium (Ti)
Titanium Nitride (TiN)
Parylene C
Everlube
PTFE(Polytetrafluoroethylene)
Phosphate passivation
multi-layer
Nickel-Copper-Nickel
Nickel-Copper-Nickel, plus Rubber
Zinc, plus Rubber
Nickel-Copper-Nickel, plus Parylene
Nickel-Copper-Nickel, plus PTFE
Tin, plus Parylene
Zinc chromate
Adhesive
Even with the same adhesive, different magnet coating will stick differently. Please choose the right plating according to your needs.